ingenierie
Des solutions techniques sur-mesure au service de votre performance
NOTRE APPROCHE DE L'INGÉNIERIE
Chez ID-Ingénierie, chaque projet suit une méthodologie rigoureuse, structurée autour de vos besoins. Nous intervenons dès la phase d’étude pour comprendre vos objectifs, concevoir des solutions techniques adaptées et assurer leur mise en œuvre jusqu’au déploiement opérationnel.
Notre accompagnement s’étend également à la maintenance et à l’évolution de vos systèmes, afin de garantir leur efficacité et leur pérennité.
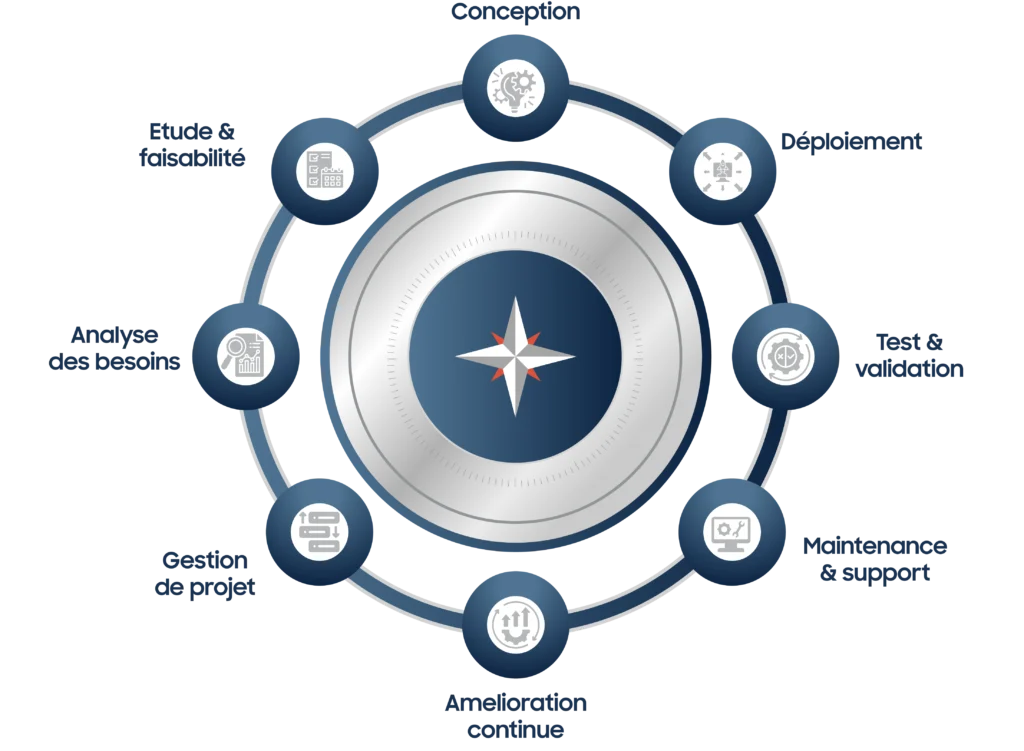
Un savoir-faire au service de votre réussite
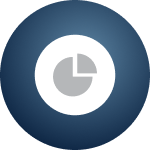
Performance
La performance, enjeu constant, influence toutes entreprises, grandes ou petites, dans un contexte économique mondial compétitif et en quête de rationalité et d’éthique.
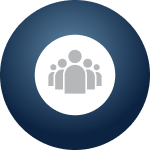
Organisation
La performance débute par une organisation adaptable, évoluant avec les technologies, le respect de l’environnement et les droits humains, au service de la progression globale.
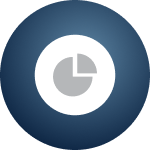
Valeur ajoutée
Chez IDI, une bonne solution naît d’une question claire. Notre expertise en ingénierie organisationnelle analyse précisément flux d’informations et actions, via dendrogrammes, pour créer des indicateurs fiables.
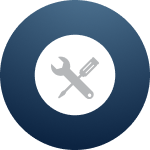
Structuration
Après analyse, nous concevons des logigrammes adaptés à vos processus, centrés sur l’humain, pour développer des outils efficaces et assurer la réussite collective.
Pourquoi choisir ID-Ingénierie ?
Chez ID-Ingénierie, nous savons que chaque projet est unique. C’est pourquoi nous concevons des solutions sur-mesure, en nous appuyant sur une méthodologie éprouvée, rigoureuse et transparente. De l’analyse initiale à la mise en œuvre, nous mettons un point d’honneur à vous accompagner avec réactivité, écoute et engagement.
Notre expertise croisée en ingénierie technique et organisationnelle nous permet d’optimiser vos processus internes, de fiabiliser vos outils, et de fluidifier la circulation de l’information. Nous prenons également en compte les enjeux humains, environnementaux et économiques de votre structure afin de construire des solutions durables, éthiques et performantes.
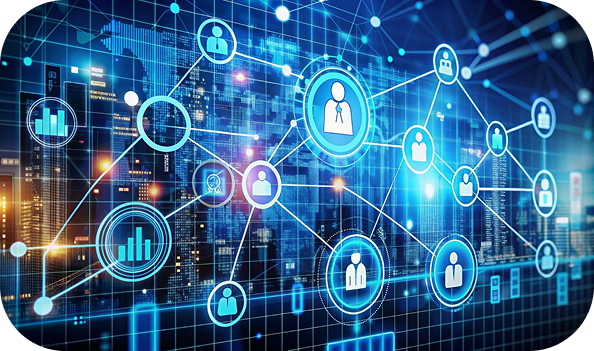